KIOGE-2018
Modern Energy Efficient Approaches to Pumping Equipment for Reservoir Pressure Maintenance (RPM) Systems
In order to improve energy efficiency of pumping equipment for RPM systems, Nasosenergomash Sumy JSC together with HMS Group JSC conducts energy audits of pumping systems (PS) and executes the modernization of PS on its basis and the customer's assignment, solving the problem of creating an optimal wet end of pump for assigned parameters, restoring and/or maintaining performance of a pump, and reducing operating and energy costs.
The implementation of these works allows to increase the efficiency, productivity and turnaround time of pump operation, to increase the reliability, to expand consumer properties, reduce energy consumption and save money on their production and maintenance.
The effectiveness of methods of improving energy efficiency, applied at Nasosenergomash Sumy JSC, has been confirmed in the course of operation of PS at oil producing companies in countries of near and far abroad.
The reduction of power efficiency of PS for RPM systems associated with the operating conditions of pumping equipment and technological features of the pumping system. The first group of factors include the underload mode (less than 70% of rated flow) and the overload (120% of rated flow); valve flow control with a significant restriction; operation without major repairs for a long period; the deterioration of the pressure characteristic by more than 10% of the nominal value; the overload of the motor working current.
The second group of factors includes the change of characteristics of a pressure system, for example, reduced injectivity of RPM system injection wells and a planned reduction in volumes of injection (pumping).
In the presence of at least one of these factors, it is advisable to conduct an inspection (audit) of PS of RPM system.
Energy audit of pumping systems
The purpose of PS energy audit is to develop and implement action plan to reduce energy consumption of PS and increase their operational reliability.
To achieve this goal it is necessary to solve a number of problems. Firstly, it is obtaining reliable data on technical condition of PS and the required system parameters. Secondly, it is necessary to conduct a full analysis of the pump operating modes and of the whole object. And finally, thirdly, test the installed equipment according to the requirements of the system and to determine the possibility of improving its efficiency.
These problems are solved, in particular, through analysis of documentation and data of instrumental measurements of operating parameters of pumping equipment.
The inspection should result in a significant reduction in the cost of electricity and the operation of PS, increase of the overhaul period (OP) of the pumping equipment and ensuring an acceptable payback period.
Energy audit is carried out in three stages. The first stage involves a preliminary study of the object, the goals and objectives of the audit are defined, documentation, technological charts, operating log, log of pumping equipment repairs, input and output parameters of the pumps and PS, and the parameters of the handled medium are examined.
The second stage is devoted to defining the operating parameters of the pumping equipment and operating modes of PS directly at the object. This is accomplished by performing instrumental measurements, Automatic Process Control System (APCS) data collection, a survey of specialists of the enterprise is conducted and the plans of management are specified.
At the third stage of the audit the information obtained is analyzed, and based on the results of the analysis recommendations to reduce energy consumption are assigned, a feasibility study of modernization is formed, costs and a payback period for pumping equipment are calculated.
Energy audit and subsequent modernization of RPM objects was held at fields in Western Siberia and included the following activities:
- inspection of modular cluster pump stations (MCPS), approval of the necessary head and rate parameters of injection;
- determination of optimal working parameters of pumps;
- production of repair kits for modernization;
- overhaul of pumps with the use of the modernization kit;
- testing and running pump on the stand;
- installation of pump at the object, adjustment work, commissioning, conducting pilot run;
- service during the warranty period, pumps technical condition monitoring.
The result of this work was the achieved increase of the efficiency and the energy efficiency of PS of RPM system (Fig. 1).
Creating an optimal wet end of pump
Today, on the basis of UHC-180 manufactured and marketed a whole range of UHC at nominal flow from 45 to 240 m3/h with the same connection dimensions. In addition, new dimension ranges developed for the nominal flow of 10, 30, 315, 500, 630 and 720 m3/h (Fig. 2).
To improve the efficiency of the pump it is necessary that the nominal point of operation of the pump is close to the desired operating point of the system. In that case, if the target point is significantly different from the optimal head and rate specification (HRS), the specialists of Nasosenergomash Sumy JSC manufacture a new wet end of pump. This work often also includes the manufacture of new wheels and guide vanes (GV), and in the process of its implementation the most modern techniques and software are used for full range of calculations, including 3D modeling of the flow parts (ANSYS CFХ, PumpLinx CFD), calculations of strength, thermal state and dynamics of the whole structure (ANSYS).
An example of upgrading to the required point of injection are pumps of UHC-315 type (Fig. 3). For connecting dimensions, they are made similar to UHC-180 pumps, which allows to replace the pump in the unit with minimal installation work.
Also at one of the inspected MCPS, UHC 240-1900 pump was replaced with UHCp 240-1900 (200-2100) with adaptation of parameters based on results of inspection (Fig. 4). As the result it was possible to increase the injection volume by 19% while reducing energy consumption by 14%. The savings in energy costs amounted to 5.36 mln RUB/year.
Recovery and (or) preservation of pump performance
Another way to increase the energy efficiency of RPM systems pumps is to recover and (or) preserve their performance.
In most cases, Nasosenergomash Sumy JSC recommends customer to replace the old equipment with a new one, but there are situations when the customer makes a choice in favor of modernization of old equipment. In this case, we perform major repairs with application of modernization kits, which includes replacement of impeller, shafts, mechanical seals, etc. (Fig. 5).
The repair allows to reduce energy consumption, increase reliability, and to enhance consumer properties of the pump by installing a replaceable flow parts. For example, in UHC-180 flow parts are installed designed for a nominal flow of 45, 63, 90, 120, 200 and 240 m3/h, as well as other custom options.
In the task of keeping the pump performance for a long time the fundamental role is played by the correct choice of the pump material. Nasosenergomash Sumy JSC offers its customers pumps in the standard, wear-resistant, abrasion-corrosion resistant and duplex (super duplex) material design (table. 1).
Thanks to the two-phase (austenitic-ferritic) structure, duplex steel in comparison with other classes of steels have higher strength, which allows to reduce weight-and-dimensional characteristics of the product, and high resistance to corrosion, especially to stress corrosion general, continuous, pitting and contact corrosion. In addition, the duplex steels is characterized by high wear and erosion resistance, high resistance to fatigue failure and low thermal expansion.
For the relative evaluation of corrosion resistance of steels it is customary to use a pitting resistance equivalent number, PREN:
PREN = %Cr + 3,3 × %Mo + 16 × %N
For the manufacture of pumps in a duplex design steel is used PREN of which is 28-30 and above, and for the manufacture of pumps in super-duplex performance – 40 and above.
Reduced operating costs
It is also possible to improve the efficiency of PS for RPM by reducing operating costs, including through the introduction of more energy efficient models of pumps, such as UHCz, UHCp and UHCDp.
In the design of UHCz pump there are pad bearing with force or crankcase lubrication system, self-regulating hydraulic offloading device (hydraulic balancing device) with the possibility of hard-alloy rings installation, end seal of the rotor of front or sealing type, with the possibility of hydroclone clean-up system installation, as well as cylindrical bearing force or crankcase lubrication system (Fig. 6).
In addition, the design of UHCz pump provides a special overlaying and coating of wear surfaces, the optimal ratio of impeller blades and GV channels providing the minimum vibro-activity of pump and unification of the size of UHC-240, 180, 120, 90, 63, 45. Reduced operating costs for UHCz pumps is achieved, primarily, through the extension of the overhaul period.
In the UHCp pump impeller located opposite ("back to back"), which allows to unload the rotor from the axial forces and to exclude hydraulic balancing device from the design of pump. Special materials and coatings of parts of wear rings provide increased resistance to erosion and wear.
The central throttle bushing improves rotor dynamics, especially with a large number of stages. Even with thw wear of the wear surfaces, the residual axial force does not change, due to the patented construction of pump (Fig. 7).
Pumps of this type on the basic parameters fully meet the requirements of GOST 32601-2013 (API610/ISO 13709). Unification for connecting dimensions to foundation and nozzle at the entrance of UHC 45, 63, 90, 120, 180, 240 is provided.
Currently, for the foreign projects, in particular for the Middle East, UHCDp double-casing pumps (BB5 type API 610) are delivered (Fig. 8). In our opinion, in the future, these pumps can be in demand by customers from the post-Soviet areas. Extractable inner housing of a cartridge type reduces the time of service at the place of operation, as it allows repair without disassembly of the casing and piping.
The outer casing is designed for a maximum pressure of the pump, and a support axis provide resistance to the effects of temperature and loads on the nozzles. Opposed location of impeller allows to unload the rotor from the axial forces and to exclude hydraulic balancing device from the design of pump. Individual mounting of each of impellers with casting ring and key protects against axial and radial displacements. Replacement rings of casing and impeller with the use of special coatings guarantee a high resistance to erosion and wear, but also reduce the cost of pump repair. UHCDp pumps fully comply with the requirements GOST32601-2013 (API610/ISO 13709).
UHCDp pumps in super-duplex design were delivered for the West Qurna-2 field in Iraq. Pump flow is 286 m3/h, head – 1388 m, capacity – 1780 kW. Pump is fully stocked on a common base frame with a motor, oil station and CMD&A system (Fig. 9). Lubrication of the bearings is carried out forcibly, the oil pump drive is carried out from the shaft of the main pump, oil is cooled by the air heat exchanger.
In conclusion, it should be mentioned that Nasosenergomash Sumy JSC carries out a continuous work aimed at creating new equipment, improving the standard designs of pumps, increasing reliability, maintainability, equipment safety, increase of its service life. We solve problems of any complexity on the creation of the modern pumping equipment of high technical level to meet individual customer requirements and we are open to suggestions for cooperation.
ILLUSTRATIONS
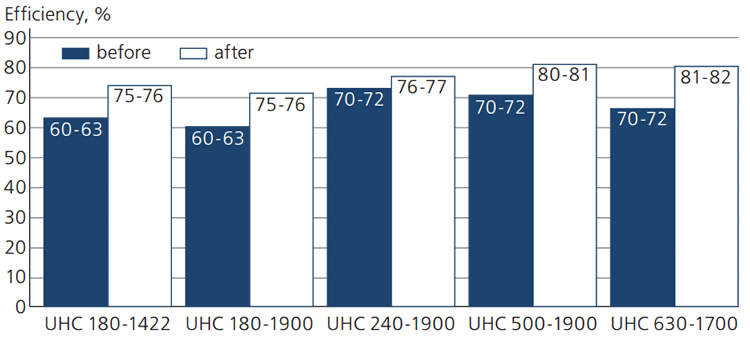
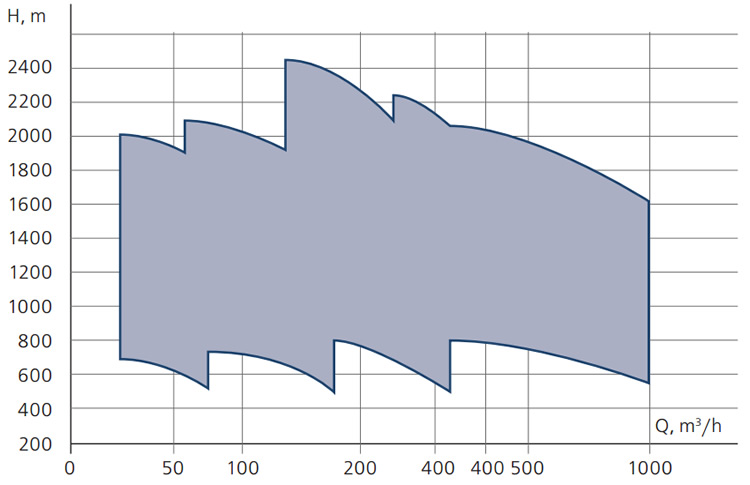
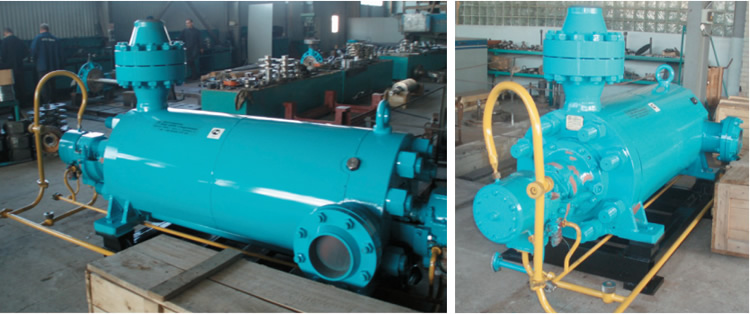
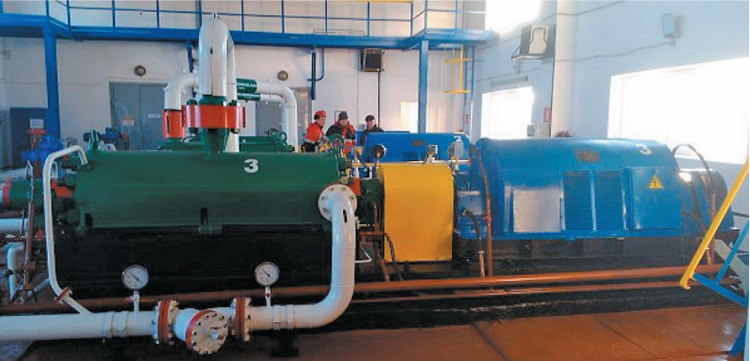
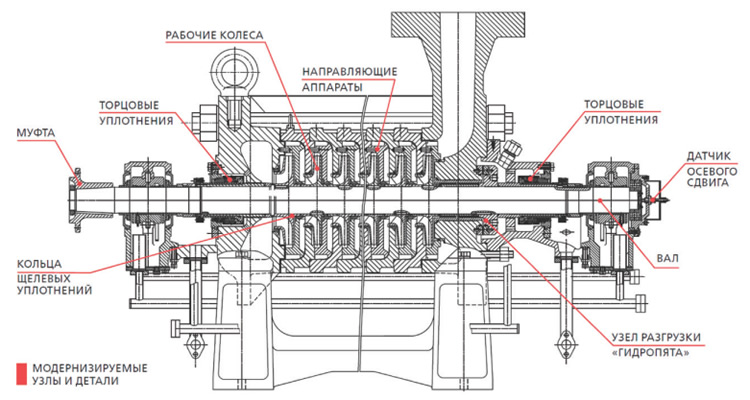
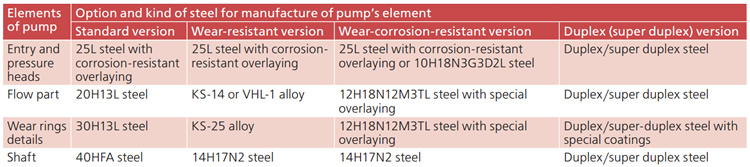
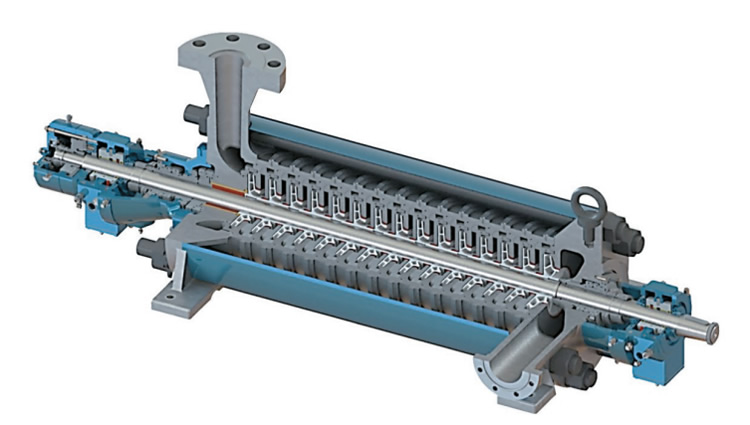
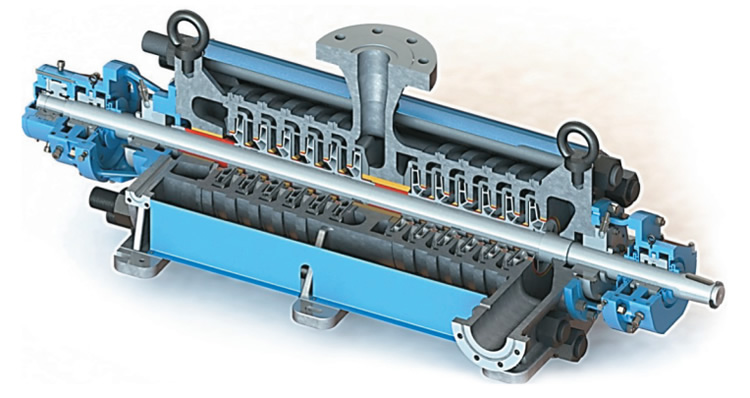
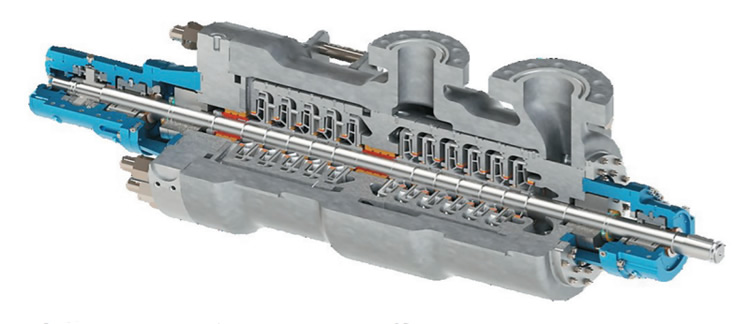
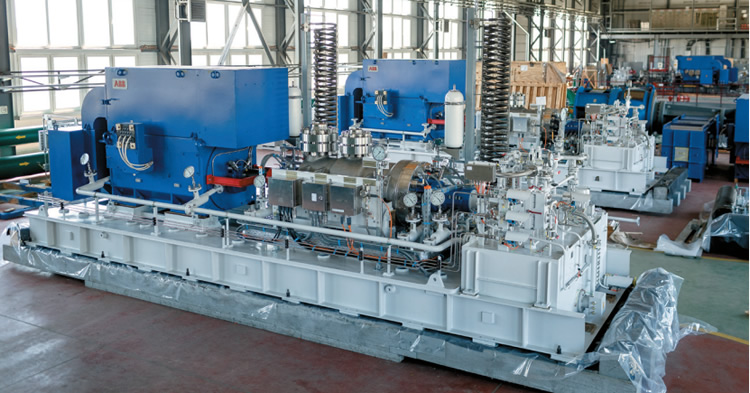