Petrochemistry and oil refining
Decarbonization. Further Steps and Practice
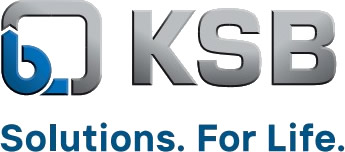
We are in the midst of a transformation into a more environmentally conscious society, one of the key issues we face is how to deal with CO2 and limit global warming. On this path, besides capturing, transporting, using and storing carbon dioxide, to reduce a harmful impact of the industrial activities on the climate, it is vital that production processes themselves as well as final products become more sustainable and climate-neutral, widely implemented and used.
Thus, in order to limit global warming to 1.5 °C, the states that ratified the Paris Climate Agreement are committed to making climatefriendly changes to their economies, including the mobility sector. Previously, fossil fuels that produced large volumes of CO2 emissions were burned. Today, however, more sustainable solutions are in demand, with carbon-neutral, nonfossil fuels becoming increasingly important.
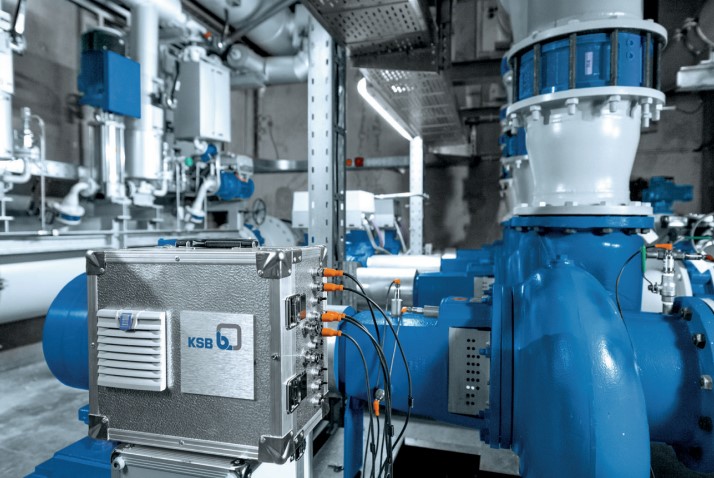
- Non-fossil fuels and synthetic fuels are gaining importance, especially in those industries in which electrification is only feasible in the long term (for example, shipping and aviation). Non-fossil fuel is mostly liquid fuel produced from biomass for use in combustion engines. Renewable raw materials such as rapeseed, sugar beet, wood, straw and residues from the food processing industry can be used as basis. The most important types of non-fossil fuels are biodiesel, bioethanol, biomethane and vegetable oil (rapeseed oil).
- Synthetic fuels or synfuels are produced from a mixture of isolated carbon dioxide and climate-neutral hydrogen. These fuels are currently in the development phase. However, they will play a major role in the future, especially in industries that are not easily electrified. Synthetic fuel is a liquid fuel obtained from the Fischer–Tropsch process, which converts a mixture of carbon monoxide and hydrogen or water vapor into liquid hydrocarbons inside the reactor. Products: ethanol, diesel fuel, kerosene, SAF (sustainable aviation fuel), gasoline, methanol.
For many years now, KSB has been active in the area of non-fossil fuels and synthetic fuels, knows the processes involved, has the expertise, experience and relevant product portfolio:
- Pumps used in fermentation and transesterification processes to operate under the toughest conditions. Thanks to their large range of seal and material variants, MegaCPK and Magnochem standardised chemical pump series are particularly suitable for aggressive fluids. In process steps involving solids-laden fluids, our KWP series impresses with its wear-resistant design and impeller variance.
- In auxiliary processes, ETA series pumps ensure reliable and efficient water transport.KSB’s Movitec, Multitec and HG series provide the necessary water pressure through their multistage design.
In addition to the extensive pump range, KSB also supplies valves that are suitable for a variety of process fluids and supply fluids. These include manual, actuated and controlled valves as well as those equipped with positioners:
- The ISORIA butterfly valve is an all-rounder. With over three million standard variants, this valve is extremely versatile.
- The double-offset DANAIS butterfly valve can also easily handle high temperatures.
The KE butterfly valves and the SISTO diaphragm valves are the right solutions for aggressive fluids or special requirements relating to emissions control.
As a full-range supplier, KSB is able to equip entire systems with the necessary pumps, valves and automation solutions. It provides products to the API and ISO standards, including mag-drive pumps, suitable mechanical seals, and lots more. Moreover, an ATEX-compliant version of the intelligent monitoring solution, KSB Guard, is available to facilitate smart monitoring of systems.
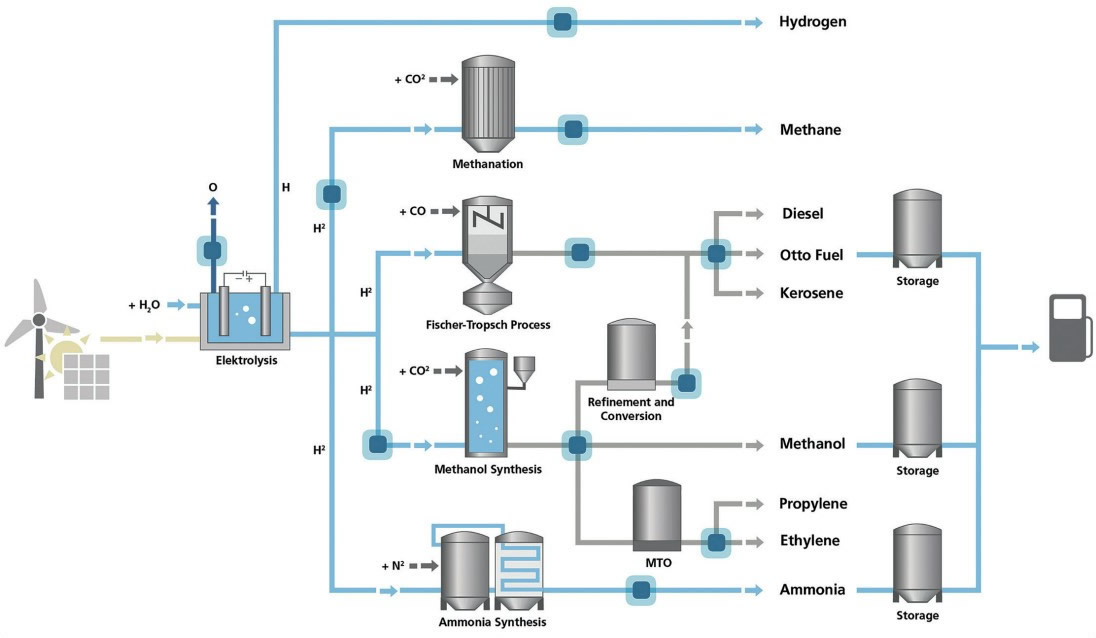
SMART SERVICE TO MAKE THE SYSTEMS MORE CLIMATE-FRIENDLY
Simultaneous transformation of technological processes and mass switch to sustainable products is a challenging task, but it can be solved step by step. The gradual modernization of existing production lines and technological processess with implementation of climatefriendly, energy-efficient solutions and equipment will allow to achieve impressive results in reducing operating costs of centrifugal pumps and CO2 emissions, forging a path to more sustainability.
For instance, old generation pumps or the pumps not optimally matched to the system consume too much energy. With KSB comprehensive system analysis this will no longer be an issue. SES System Efficiency Service for pumps and systems offers the customers detailed insights into the pump installation which serve as a basis for optimising the energy efficiency of the pumps and systems. This saves energy costs and reduces CO2 emissions.
A data logger takes measurements on site and records process variables and vibration levels to determine the pumps’ operating behaviour. A mobile device is used to measure the effective power in the control cabinet in order to determine the pump’s efficiency and to assess deviations, such as those arising from wear. This allows KSB to determine the actual load profile of the pumps and compare this with the design conditions. The aim is to identify potential savings and causes of any damage. After measurement and analysis with SES System Efficiency Service, the operator gets detailed overview of the current energy efficiency of the pumps and systems. On this basis, KSB makes recommendations for increasing energy efficiency. As well as making the operation of the pumps and valves more sustainable, this also significantly lowers their life cycle costs.
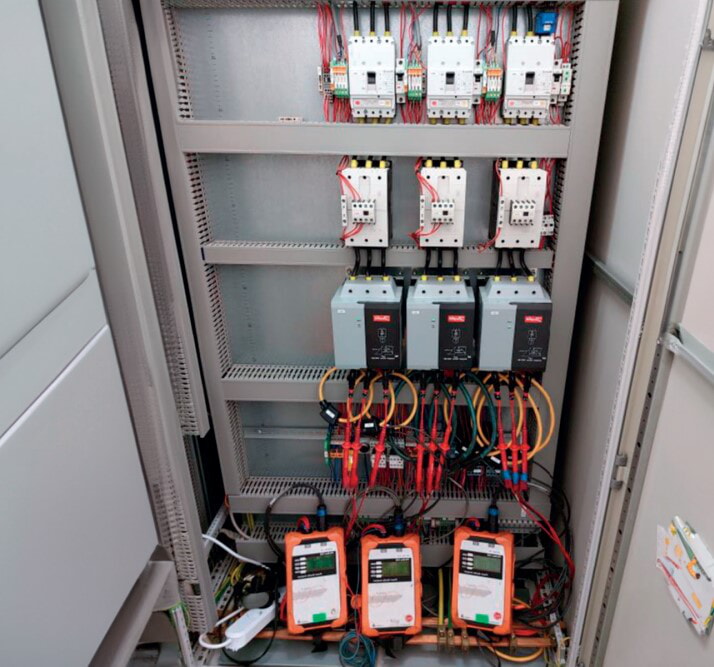
Practice. SES in chemical production: full performance, half the energy costs
In Germany, a global manufacturer of different chemical products operates a plant producing synthetic resins and synthetic resin dispersions. In 2022, experts from SES System Efficiency Service were commissioned to investigate the cooling water systems of the two production buildings to uncover potentials for optimisation and find ways of tapping into them.
The cooling water system’s pump system to be investigated is divided into two groups of pumps that are connected with each other. Pump group 1 is made up of three pumps of the type Etanorm – two of them operated at fixed speed and one at variable speed. Pump group 2 is made up of two Etanorm pumps – one operated at fixed speed and one at variable speed. The pumps are fitted with drives of different sizes, ranging from 30 to 45 kW.
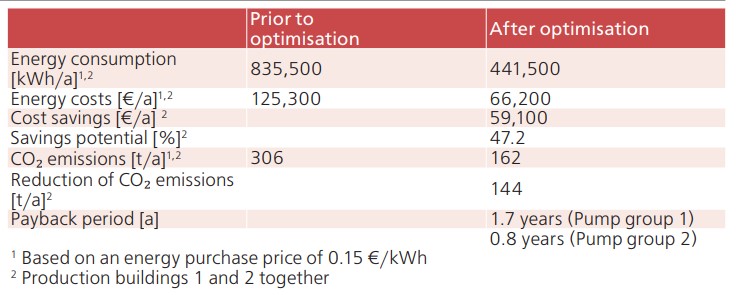
The SES System Efficiency Service experts were commissioned to analyse the system in depth and identify optimisation opportunities.
The KSB experts conducted a number of measurements at different points, including inlet pressure and discharge pressure, speed, flow rates and other variables. The results revealed:
For normal operation of pump group 1:
The pumps’ flow rate was between 0 and 465 m3 /h; control pressure of the collecting line - 5 bar; the pressure at bad-value point fluctuates between 0.5 and 3.2 bar.
For normal operation of pump group 2:
Flow rate between 80 and 200 m3 /h; control pressure of the collecting line - 6 bar; the pressure at bad-value point fluctuates between 1 and 4.6 bar.
Also, some problems had occurred in the system: Pressure losses were caused by the lift check valves installed as they were too small. Some of the motors were running at their ratings limit. Frequent pressure drops were observed, that can be linked to various causes, such as operating a mix of fixed speed and variable speed machinery.
Based on an electricity price of 0.15 €/kWh and the previous operating parameters, the energy costs amount to over € 125,000 per year.
KSB’s experts suggested upgrading the system and using new, variable speed motors. The following optimisation concept was offered to the customer:
- Increasing the pipe diameter between pump and collecting line to DN 150.
- Replacing the current swing check valves and changing their installation position.
- Using pumps with impellers of maximum impeller diameter (219 mm).
- Using new motors with frequency inverters of at least 45 kW for three of the five pumps.
- KSB’s engineered pump control system incl. frequency inverter, PLC with KSB software module for optimum pump operation.
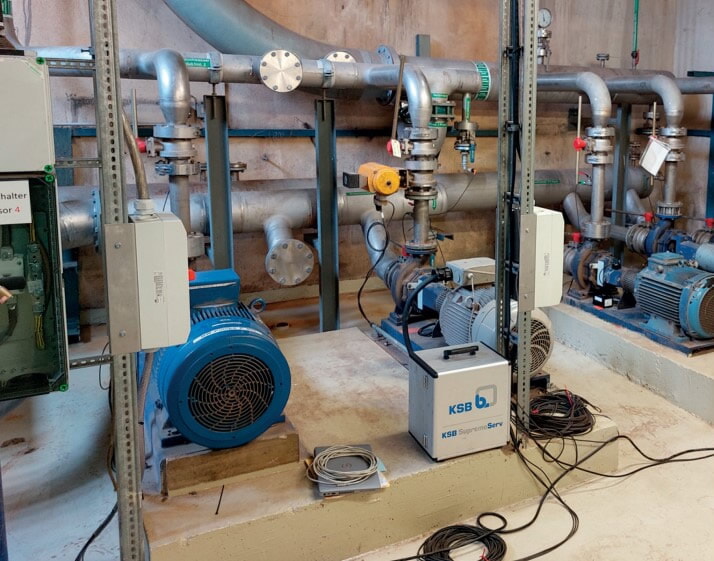
The customer decided to implement the suggested measures and now benefits from the following:
- In single-pump or dual-pump operation all operating points of PG 1 are covered in an energy-efficient manner.
- A higher pressure is available in the system, and one pump is always on standby.
- All operating points of PG 2 can now be covered by a single pump.
- Speed control enables operation over the entire system curve. In conclusion: higher system availability at constant pressure for all consumers.
- Significant reduction of life cycle costs.
- Massive energy savings equalling close to 50 %.
- Marked reduction of CO2 emissions (almost 150 tonnes per year).
- Plus a clearly enhanced operating reliability.
Energy savings compared to current operation: almost 50% equalling € 59,100 per year.
This practice discovers the potential and advantages of the systems optimization as a whole and importance of the system approach.
Thanks to technical excellence and passion for innovative solutions in the area of eco-friendly technologies, system approach to modernization of the existing projects, KSB is making an important contribution towards greater sustainability and therefore a better future.