The Issue’s Focus: Caspian
High Temperature Resistant Polyethylene – New Solution for Oil and Gas Industry
Corrosion of steel pipes is a serious problem for the oil and gas industry; it requires frequent pipe
replacement and causes additional spending. In some cases, steel pipes can be substituted with corrosion resistant polyethylene pipes. However, a standard HDPE 100 pipe cannot be used in extreme temperature conditions. Therefore, a solution is pipes made from high temperature resistant polyethylene. Their physical and chemical structure allows for transportation of aggressive fluids, including condensate gas and produced water.
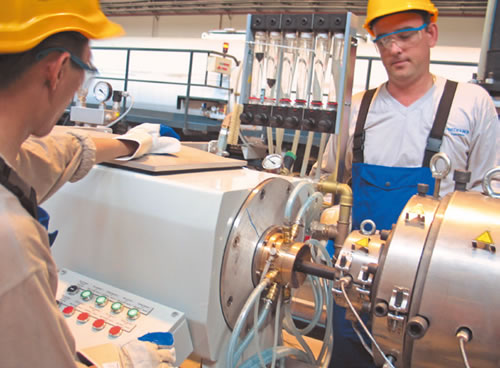
Today, Chevron is successfully deploying the new generation of thermoplastics in Kazakhstan – Polyethlylene of Raised Temperature Resistance (PERT). Among pipes made from this material monolayer PERT pipes stand out for broad temperature ranges. They are one of the most popular products of Chevron’s Polyethylene Pipe Plant in Atyrau (APPP).
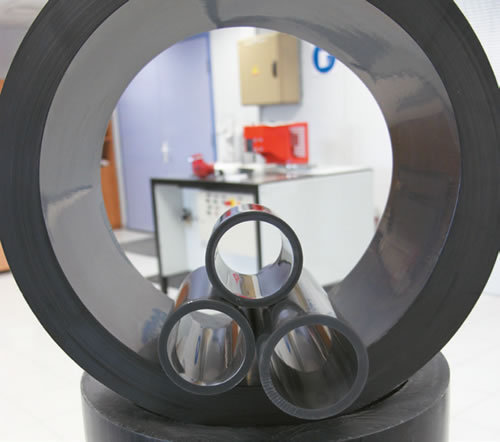
Main advantages of the thermal resistant plastic:
– Broad temperature ranges from
-40°С to +95°С;
– No corrosion and deposits;
– Ease in installation, welding or
all coupling types are possible;
– Elasticity;
– High recovery rates;
– Low surface roughness;
– Long lifetime;
– Zero operational costs;
– Chemical resistance;
– Recyclability;
– High ageing resistance;
– Can have multiple layers,
including diffusion layer;
– Can be supplied in sections or in
drums of different diameter to cut costs.
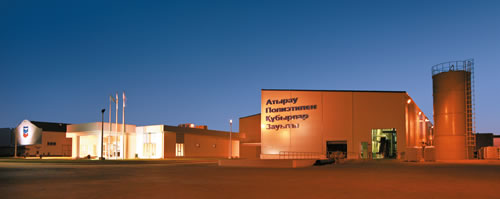
Pipes are manufactured in accordance with ST RoK GOST R 52134-2010 and ST RoK 2594-014 standards. Pipes can be used in extreme temperatures and under high pressure. The plant produces these pipes with the diameter of up to 1200 mm. Socket welding, butt welding,
electrofusion welding and flange connections are applicable for pipes of high-thermal-resistance polyethylene. They can also be used for manufacturing of welded products such as bends and tees.

FACTS
In 2012, pipes produced by APPP were supplied to TCO for Water Injection System Upgrade Project (produced water).
The water at Tengiz oil field is highly corrosive and rich in sulfur. Polyethylene pipes (as
opposed to steel pipes) allowed for increase of 10 times in the lifetime of pipelines – from 5
to 50 years. It also reduced operating costs (for instance, it cut expenses related to use of
cathodic protection and corrosion inhibitors in steel pipes) and minimized the need for visual
inspections.
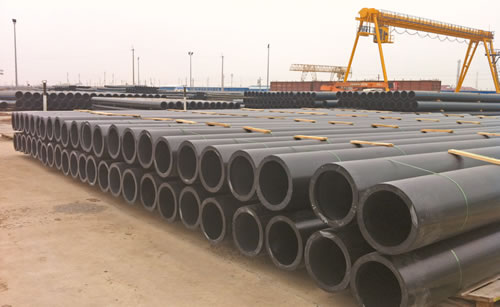