Фокус номера: российский вектор
Мировые стандарты ООО «Газпромнефть-СМ»
В начале апреля на Омском заводе смазочных материалов (ОЗСМ) была введена в эксплуатацию II очередь комплекса по смешению, затариванию и фасовке масел. С вводом высокотехнологичного комплекса производственная мощность завода составила до 300 тыс. тонн смазочных материалов, включая фасовку 180 тыс. тонн готовой продукции. Новый комплекс в Омске создавался в два этапа.
В мае 2012 года были введены в эксплуатацию объекты I очереди, предназначенные для производства тары и фасовки, склад сырья и готовой продукции, а также сверхсовременный резервуарный парк. В рамках II этапа построена полностью автоматизированная станция смешения масел. Инвестиции в создание комплекса составили порядка 3,4 млрд руб. Автоматическая станция смешения масел является ключевым элементом комплекса. И если говорить о смешении, фасовке, логистике, то с вводом в эксплуатацию II очереди, производственный комплекс полностью сформирован. Таким образом, нет больше ограничений по смешению и производству - все виды продукции, которые сегодня востребованы на рынке, завод может произвести.
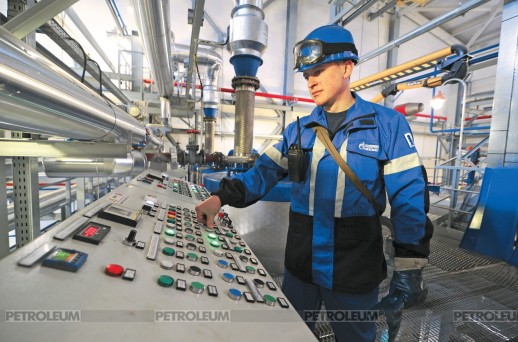
Станция смешения масел оснащена английскими смесителями фирмы Silver Stone. На сегодняшний день это самое современное оборудование в отрасли. Оно позволило существенно сократить время и контакт масла. В процессе производства очень важно не перегревать и не окислять продукты. И на ОЗСМ достигли прекрасного результата – в два раза сократили время приготовления партии, что позволило маслу не окисляться в процессе производства.
Оно имеет меньшую температуру при приготовлении и, соответственно, лучшие функциональные характеристики, в отличие от других продуктов. При работе смесителей Silver Stone создаётся мощный вихревой поток, который обеспечивает очень быстрое растворение полимерной присадки, сокращается время окисления продукта, что позволяет очень быстро переходить из одной группы масел в другую, с одного продукта на другой, при минимальных потерях времени. Это позволяет экономить электроэнергию, обеспечивать энергосберегающие технологии и тем самым иметь низкую себестоимость продукции, что дает конкурентные преимущества на рынке.
Что касается рецептур, то их в систему загружено 70 видов. Смена рецептур, находящихся в базе, происходит каждый день. Командой на операционном мониторе можно выбрать из банка данных определенный вид, и система начинает готовить соответствующие продукты. На заводе используются рецептуры как ведущих мировых компаний, так и собственного производства. На всех трех заводах ООО «Газпром нефть» – в Ярославле, Подмосковье (г. Фрязино) и Омске – есть лаборатории, которые занимаются исследованием и разработкой.
В Москве все это интегрировано в общий центр научно-исследовательских разработок и продвижения продукции. Этот центр опирается на исследовательскую часть, которая находится непосредственно на предприятиях, при поддержке отраслевой науки и изучения опыта лидеров в области технологий. В Москве находится центральный аппарат исследовательского центра, а наука и все ресурсы сосредоточены на предприятиях. Это позволяет разрабатывать новые рецептуры, а также большое количество продуктов. В 2013 году компания приступила к разработке собственных технологий. А работа с такими ведущими автопроизводителями, как Mercedes Benz Trucks Vostok, ГК «Автотор» (для автомобилей General Motors), АК «Дервейс» и т.д. позволяет инвестировать в технологии, которые принадлежат только «Газпромнефть-СМ», и в течение какого-то периода компания будет эксклюзивно ими пользоваться.
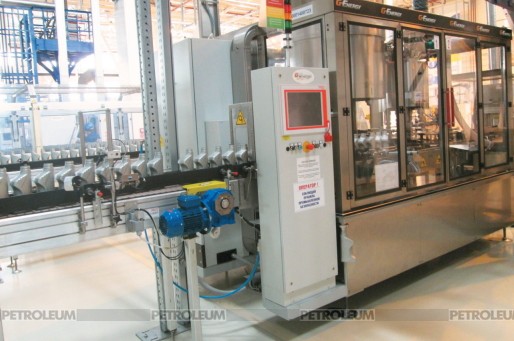
Готовая продукция Омского завода смазочных материалов включает свыше 500 наименований масел и смазок (1200 товарных позиций). Эти продукты соответствуют международным стандартам, а также одобрены ведущими производителями техники и оборудования. Они производятся под тремя брендами: G-Energy, «Газпромнефть», а также судовые масла под брендом Техасо, выпускаемые по лицензии компании Chevron.
На заводе хранится 1000 тонн базовых масел и 2500 тонн присадок в наливе, а также существует возможность хранения 800 тонн присадок в специальном складе – это присадки в бочках. Компания «Газпромнефть-СМ» при производстве смазочных материалов использует пакеты присадок мировых лидеров по разработке технологии товарных масел Lubrizol, Afton Chemical, Chevron Oronite, Infineum. Современные пакеты присадок являются сбалансированной композицией множества компонентов – детергенты, дисперсанты, противоизносные и противозадирные компоненты, антиоксиданты, антипенные и антикоррозионные и т.д
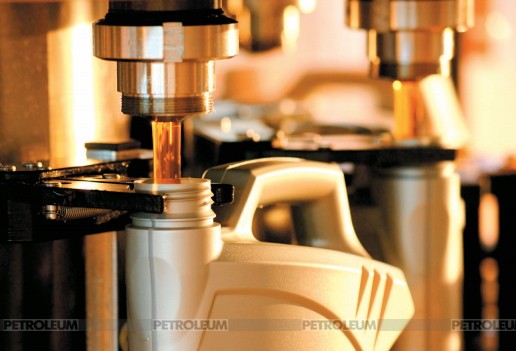
В 2012 году был введен в эксплуатацию новый комплекс фасовки мощностью 180 тыс. тонн. Три года назад была одна линия, на сегодняшний день их уже три. Компания интегрировала в эту линию еще одну станцию налива, и тем самым были увеличены мощности. Сегодня они уже достигли 200 тонн в смену. Для собственного производства тары есть две выдувные машины. От выдувной машины и до склада вся продукция вырабатывается в автоматическом режиме. Она фасуется в автоматическом режиме (налив), далее происходит автоматическая закрутка крышки, каждая канистра проверяется на герметичность, на корректно закрученную крышку, затем она подходит к узлу, где наклеивается этикетка. После этого система Wrap Round обертывает канистры, т.е. робот подает определенное количество канистр, термоклеем склеивается вся поверхность и дальше робот штабелирует их в паллеты. Паллеты оборачиваются термоусадочной пленкой, и на склад попадает готовое отгрузочное изделие – отгрузочная единица в паллетах.
Склад готовой продукции нового комплекса ОЗСМ рассчитан на единовременное хранение фасованных масел объемом 10 тыс. тонн, или 13 330 паллета-мест с автоматизированной системой SAP WMS, обеспечивающей автоматизацию и оптимизацию всех процессов складской работы. Это адресная система хранения продукции на складе. У каждой паллеты есть свой адрес. При поступлении продукции с производства на нее наносится штрих-код. После того, как сканер сканирует штрих-код, ВМС-система определяет место, где будет храниться данная продукция. У каждого водителя-штабелера имеется компьютер и сканер. При помощи сканера он производит сканирование штрих-кода, и компьютер определяет, куда эту продукцию поставить. Пронумерован каждый стеллаж и каждая паллета. Также производится отбор продукции на отгрузку. Задание приходит водителю штабелера на компьютер, при помощи сканера он производит отбор продукции.